Inventory & Receiving
The Inventory module is closely integrated with the Receiving functionality of the Purchasing Management module. This integration allows for receiving entries to count as Stock entries for items, therefore, as you create orders and receive them, the theoretical on-hand quantities will be incremented.
Take note that ordered units are not always the same unit that you will inventory by. Often times, a conversion will take place during receiving that will translate ordered units into inventoried units. For example, Item A is ordered by the case but inventoried by the individual units contained in the case, say 24. Therefore, if you order 10 cases of Item A and receive all 10 ten cases, you’re inventory stock count will equal 240.
Use the information below to gain more insight and steps to take when receiving items that are inventoried.
The first step when receiving is to set the Received Date and Valid Inventory Period. The date you select must be within the window of an Open Inventory Period.
Item Ordered by the case, but counted in Pounds, set outer count to weight in the case. In this example the outer count is 10 for 10Lbs.
Items ordered by weight and counted in weight should leave outer count set at 1. In this example the Ham was shipped 19.13 LBS, and we want to put 19.13 LBS. in stock, so the outer count remains 1.
Substitutions should be linked to your master inventory item. When an item is substituted it should be mapped to the Master inventory item. Leave the inventory item toggle switch in the off position and select the master item link to associate the substitute item to your master inventory item.
For new items, or items that you want to start tracking separately, you can toggle the Master Inventory item flag to the “On” position. Don’t forget to set the correct Outer Count to reflect your Inventory UOM.
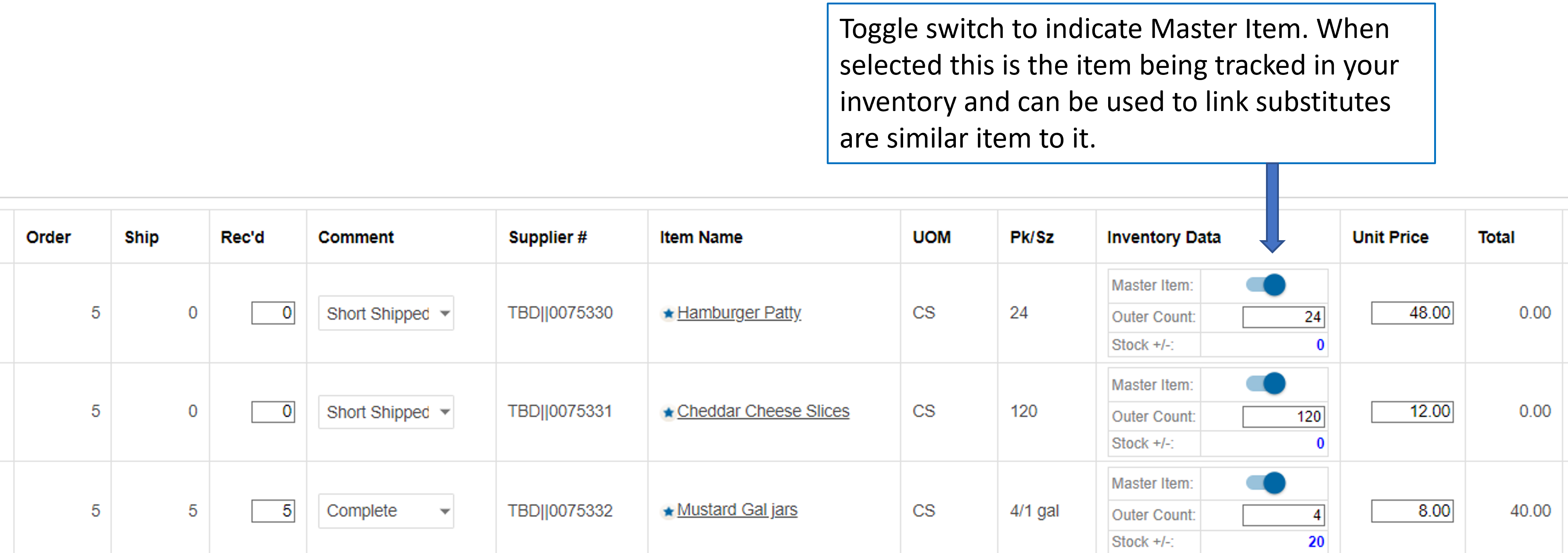